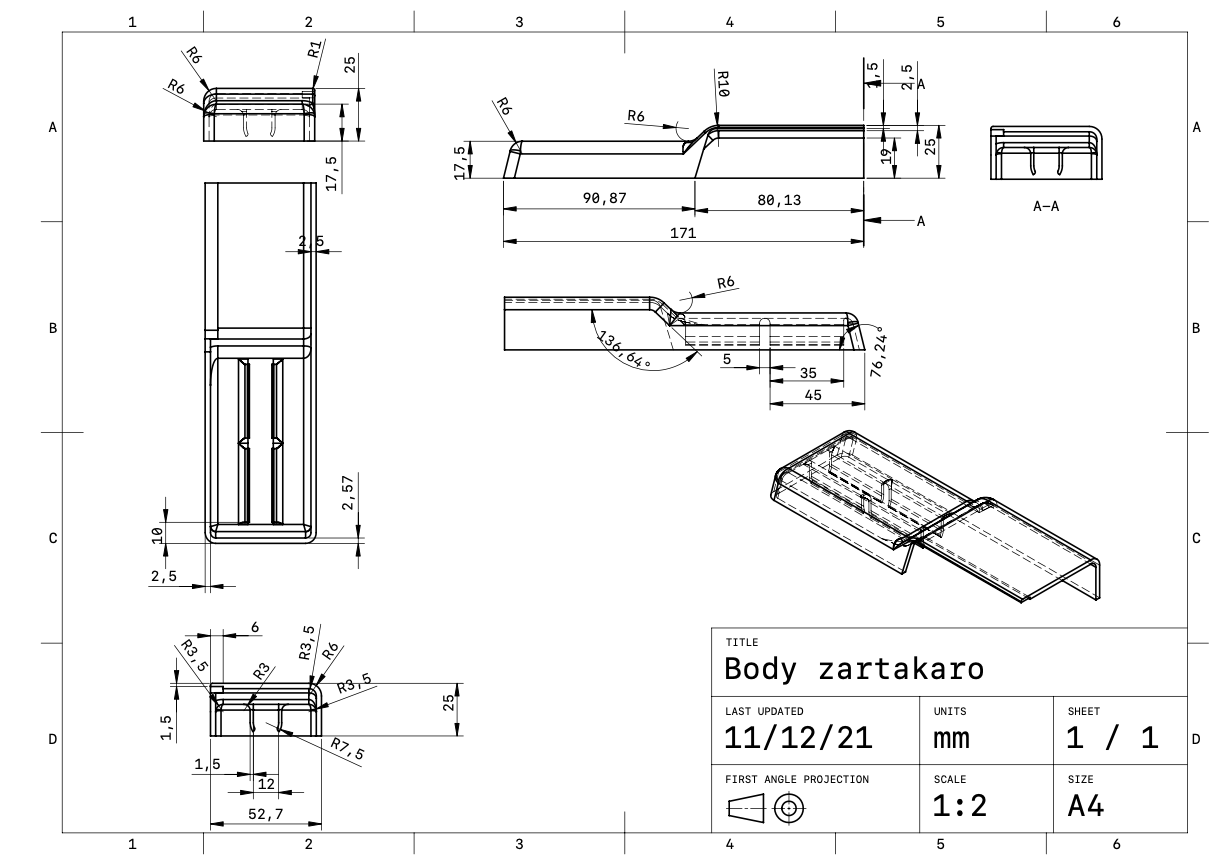
Additív FFF technológiával gyártott alkatrészek sikeres tervezésének alapjai
Mikor érdemes FFF 3D nyomtatást használni és miért?
Forrás: Ultimaker.com
Az olvasztott filament gyártás (FFF) joggal érdemelte ki helyét az egyik legelterjedtebb 3D nyomtatási technológiaként - kiküszöböli a közös tervezési korlátokat, bevezeti a tervezési rugalmasságát és a könnyű használhatóságot. A 3D nyomtatás eredményessége és a siker biztosítása érdekében azonban fontos megérteni és támaszkodni az FFF tervezés bevált gyakorlataira.
Először is bontsuk fel az FFF 3D nyomtatás előnyeit és hátrányait, valamint hasonlítsuk össze a gyártás más formáival.
FFF 3D nyomtatás kontra CNC gépek
A számítógépes numerikus vezérlő (CNC) gépek kódolt és programozott utasítások segítségével automatikusan anyag letávolításával hozzák létre az alkatrészeket. Az FFF 3D nyomtatás három kulcsfontosságú területen felülmúlja a CNC-t:
- gyors átfutási idő kis mennyiségek esetén, rövidebb gyártási munkafolyamatok és összetett alkatrészek egyszerűbb előállítása,
- kisebb szériák gyártásánál, ahol megfelelőek a műanyag-, akár kompozit tulajdonságai, nincs szűség a CNC vezérlésre használt szerszámpályák, G-kód vezérlés megírására, nyomtatókat a szeletelőprogramon keresztül vezéreljük,
- ahol a tervezett termék végellenőrzése érdekében szűkség van prototípusok, próbadarabok gyártására, a kész CAD tervek azonnal kinyomtathatóak.
FFF 3D nyomtatás kontra fröccsöntés
A fröccsöntés értékelése során az FFF 3D nyomtatás kiemelkedik az egyszerűség miatt - mind a költségek, mind a tudás tekintetében.
- A fröccsöntéshez a több száz folyamatparaméter és a tervezési korlátok miatt jellemzően csak gyakorlati tapasztalattal kell rendelkezni.
- A fröccsöntéssel ellentétben az FFF 3D nyomtatáshoz nincs szükség költséges öntőforma létrehozására, eszközök karbantartására, és lehetővé teszi a tervezés gyors és egyszerű módosítását, az új tervezés akár órákon belül rendelkezésre áll.
- A fröccsöntés legnagyobb előnye a 3D nyomtatással szemben, hogy nagy mennyiségű alkatrészeket jóval rövidebb idő alatt állíthatunk elő simább felületekkel.
FFF tervezési szempontok
A 3D nyomtatáshoz tervezés során bevált gyakorlatok állnak rendelkezésre, amelyek segítségével a legtöbbet hozhatja ki 3D nyomtatójából az általa készített alkatrészekből. Javíthatja a nyomtatási sikereket, csökkentheti a gyártási költségeket és felgyorsíthatja termékfejlesztési ciklusát.
Vegye figyelembe az építési munkatér méreteit
A 3D nyomtatott alkatrészek csak akkorák lehetnek, amekkora a nyomtató munkatere. Az Ultimaker S5 330 x 240 x 300 mm (13 x 9,4 x 11,8 hüvelyk) méretű, ami elég a felhasználók alkalmazásainak körülbelül 80%-ához, miközben megőrzi a nyomtatott alkatrész méretpontosságát. Ha egy alkatrész túl nagy, javasoljuk a modularitás használatát (alkatrészek tervezésénél érdemes a nyomtató munkaterét figyelembe venni, ha szükséges bontsa részekre az alkatrészt). Csatlakozó felületik kialakításához használja jól bevált technikákat, (pl Snap Fit Joints For Plastics). Használjon egy időben több 3D nyomtatót, a moduláris kialakítással egyszerre két részt nyomtathat különböző gépeken.
Még a nyomtatás előtt el kell dönteni az orientációt
Mivel az FFF 3D nyomtatás rétegről rétegre történik, a nyomtatott alkatrész tulajdonságait befolyásolja a nyomtatás tájolása, mely meghatározza a nyomtatás szálirányát, a belső kitöltés geometriáját, sűrűségét, raszter háló felépítését. A mechanikai tulajdonságok anizotrópok, ami azt jelenti, hogy irányuktól függően eltérőek. Az alábbi kép azt szemlélteti, hogy a szakítóvizsgálati mintát szálirányban nyomtatva szakítószilárdsága erősebb lesz, mit ha arra merőlegesen tájoltuk volna a nyomtatás irányát.
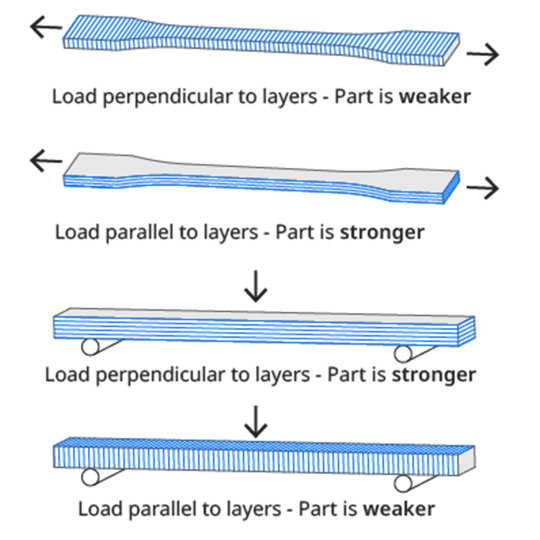
A nyomat tájolása közvetlenül befolyásolja a késztermék mechanikai tulajdonságait - és azt, hogy a modellnek szüksége lesz-e támaszanyagra. Továbbá befolyásolhatja a teljes nyomtatási-, a hordozóanyag eltávolításához szükséges utófeldolgozási időt és bizonyos oldalak felületi minőségét.
Támaszanyag használatának szükségessége
Az FFF nyomtatott részek 45 fokig önhordóak, ami eltér a többi 3D nyomtatási technológiától, amely minden szöghez támasztóanyagot igényel. A 45 fok alatti túlnyúlásokat alulról alá kell támasztani tartóanyaggal.

Kövesse az áthidaló geometriára vonatkozó irányelveket
Az áthidalás az, amikor az Ultimaker nyomtatónak a levegőben kell kinyomtatnia a modell lapos, vízszintes részét. Bár egy ilyen alkatrész tartószerkezete megoldást jelenthet, gyakran csak áthidalja a rést támaszték nélkül, funkcionálisan nem használható, mivel terhelést nem fog elviselni. Általános szabály, hogy a legtöbb alapvető filamentum esetében az FFF-nyomtatásnak nincs szüksége támaszanyagra, amikor az áthidalás mértéke 10 mm-en belül marad. Fontos azonban megjegyezni, hogy aktív hűtéssel és egyéb optimalizálási beállításokkal akár 25 mm-t is áthidalhatunk pl. Tough PLA segítségével egy Ultimaker 3D nyomtatóval.
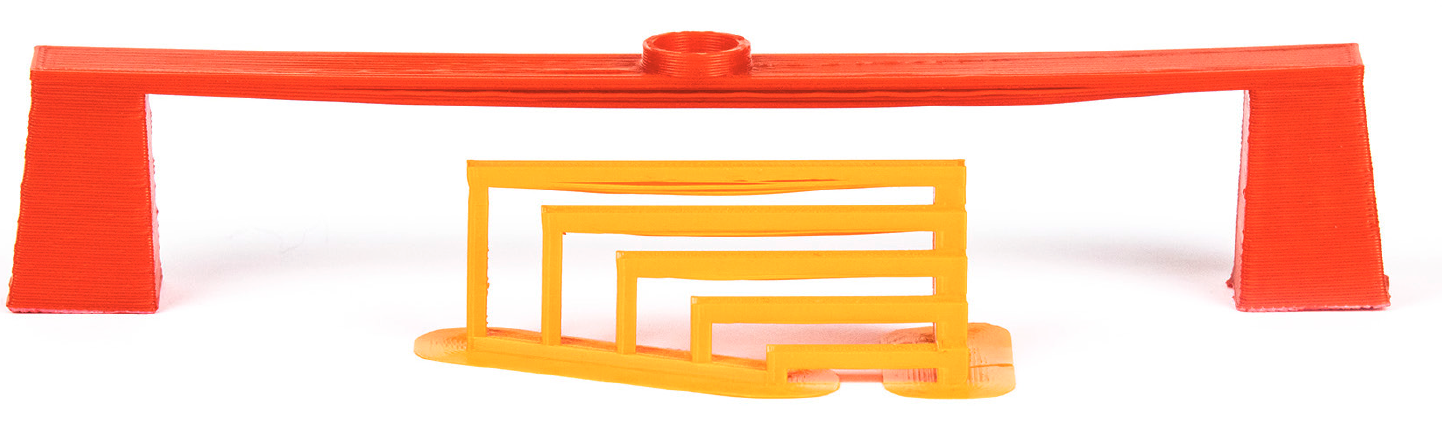
Ügyeljen a fúvóka méretére

Tervezés a furatátmérők figyelembevételével
A minimális furatméret az anyagtól és a beállításoktól függ. A legkisebb lyukra, lyukakra vonatkozik, amely támaszanyag feltöltése nélkül nyomtatható. Alapszabály, hogy a 3D nyomtatott lyukak nem lehetnek kisebbek 2 mm-nél. Ha pontos furatok szükségesek, akkor javasolt a furatokat kisebb átmérővel tervezni, és utómunkával a megfelelő méretni fúrni. Ha két vagy több alkatrészt nyomtat együtt, alkatrészek közti minimum hagyjon 0,6 mm-es távolságot, így nyomtatás végeztével a tárgyasztalról sérülésmentesen eltávolíthatóak a kész alkatrészeket.
Kerülje az éles sarkokat
Nyomtatott szálak folytonossága érdekében az éles sarkokat érdemes lekerekíteni. Lekerekítés csökkenti a vetemedés lehetőségét, mely az anyag vissza hülésével jön létre. Ha a modell funkciója megengedi, minden sarkot, érintkező felületet kerekítsen le, ezzel elősegíti a nyomtatás irányváltásának folytonosságát. Így a szálak futása, az anyag felépítése homogén és egyenletesebb lesz.
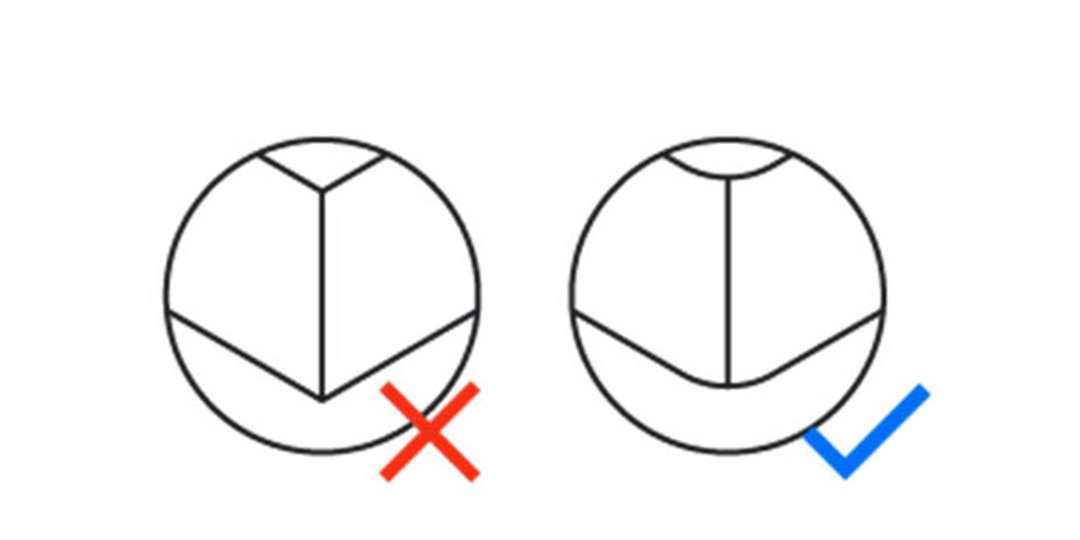
Csökkentse minimálisra az "elefánt lábát"
Raft nélküli nyomtatáskor (a 3D nyomat első vízszintes szála) az első réteg valamivel nagyobb lehet, mint a többi. Ez az "elefánt lábának" (eső réteg vastagabb lesz, mint a többi) nevezett jelenségnek köszönhető. Bár ritkán észrevehető, csökkenti a funkcionális prototípusok toleranciáját. Egy kis 45 fokos letörés (átmeneti él) hozzáadásával a nyomat alsó széléhez mérsékelhető az elefánt lábának hatása. Szelető programokban ez beállítható!
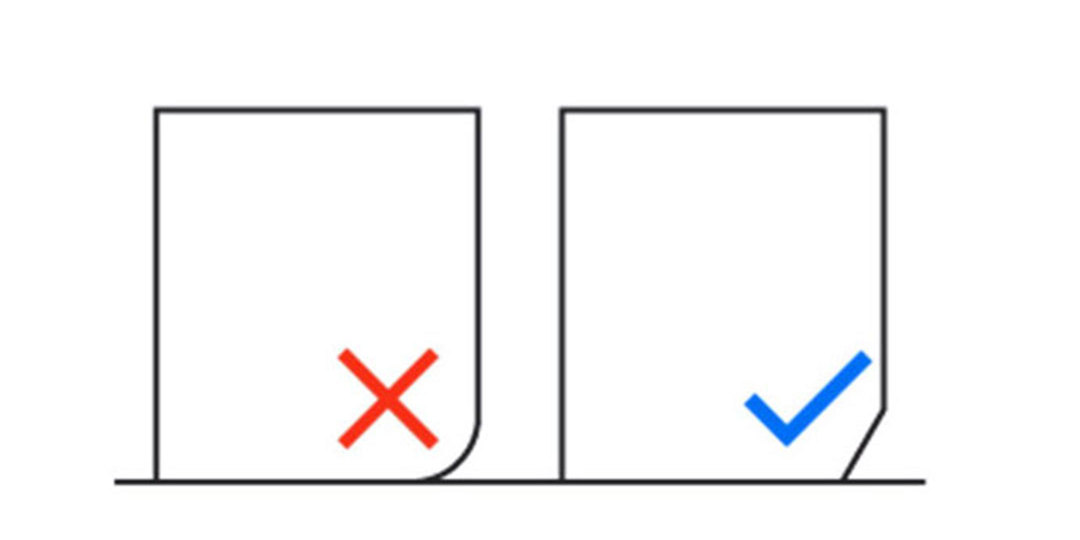
Esztétika
A vizuális prototípusokkal és a végfelhasználású alkatrészekkel szemben általában magasabb esztétikai követelményeket támasztanak. A részletesebb nyomtatás hosszabb nyomtatási időt jelent. A kisebb fúvókaméret választásával több részletet érhet el, de a nyomtatási idő is megnő.
A fenti kép egy modell három változatát mutatja, különböző rétegvastagságokkal nyomtatva. A bal oldali nyomtatás 7 óra 27 percet, a középső nyomat 3 óra 46 percet, a jobb oldali pedig csak egy 1 óra 47 percet vett igénybe.
Kitöltési sűrűség
A kitöltési sűrűség határozza meg a nyomat belsejében használt műanyag mennyiségét. A nagyobb kitöltési sűrűség azt jelenti, hogy több műanyag van a nyomat belsejében, ami erősebb tárgyat eredményez. A vizuális célú modelleknél 20% körüli kitöltési sűrűséget alkalmaznak, a végfelhasználású alkatrészeknél nagyobb sűrűség használható, általában 40%
Kitöltési vonaltávolság
A kitöltési sűrűség százalékos beállítása helyett a vonaltávolság is beállítható. Ez határozza meg az egyes kitöltési vonalak közötti távolságot, aminek ugyanolyan hatása van, mint a kitöltési sűrűség megváltoztatásának.
További modellezési tippekért és trükkökért, beleértve az alkatrész-követelményeket, az anyagok kiválasztását és a CAD-modellezéssel kapcsolatos információkat, keressen bennünket bizalommal!
Célunk, hogy a technológia iránt érdeklődő szakemberek a külföldi példa által meg- és felismerhessék a lehetőségeket!
2022.10.10. Forrás: Ultimaker.com
Esetleges fordítási hibákért elnézést kérjük, azokért felelősséget nem tudunk vállalni.