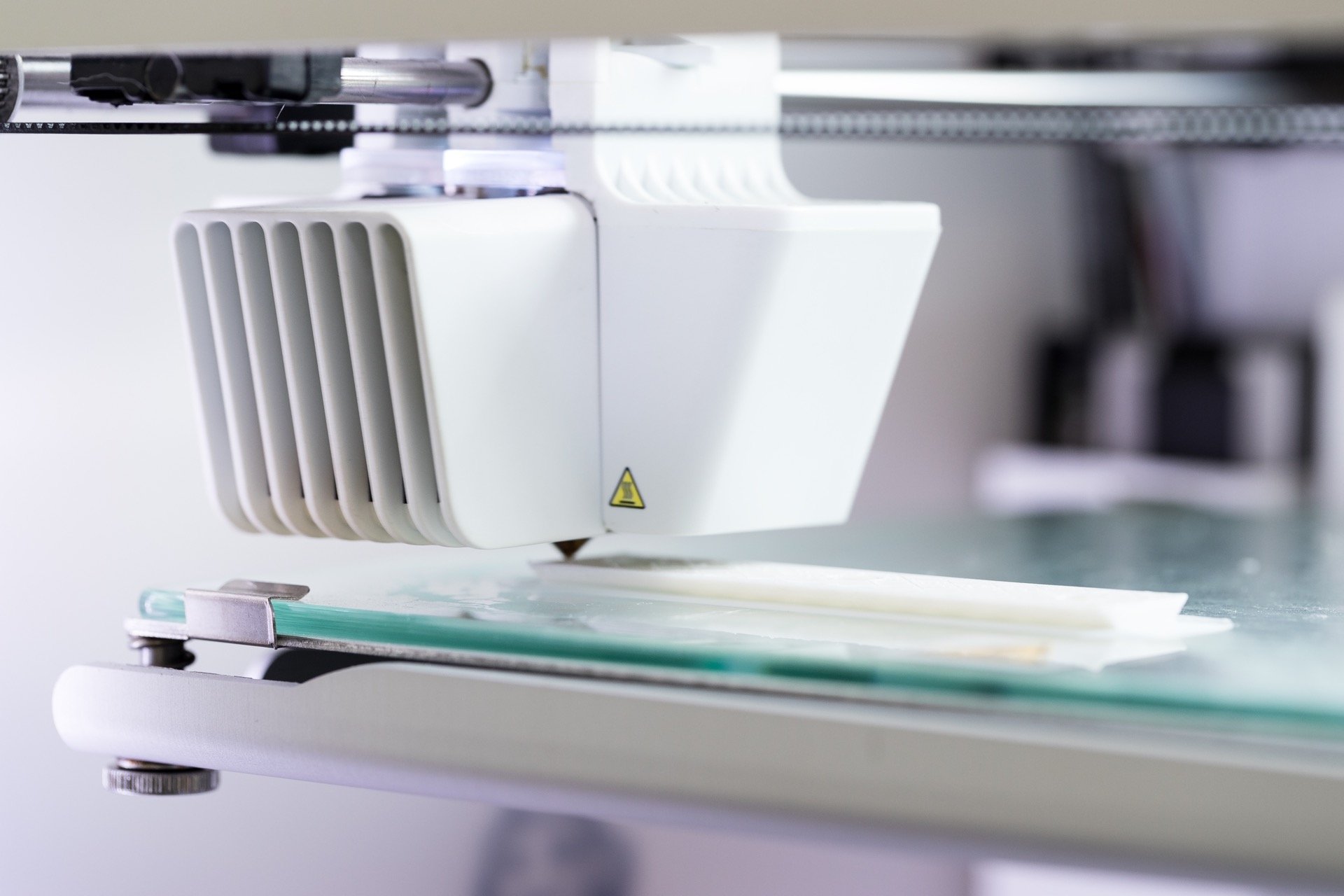
"Mennyire erősek a 3D nyomtatott alkatrészek?"
12 tonnás tartály emelése műanyag 3D-nyomtatott alkatrésszel
FFF nyomtatás határainak feszegetése
Forrás: Ultimaker.com
A fenti kérdést teszik fel a legtöbben a mérnöknek, amikor a 3D nyomtatást fontolgatják. Végül is döntő fontosságú, hogy az additív gyártásért felelős mérnök tudja, mi lehetséges a rendelkezésére álló eszközökkel. Az Ultimaker, a Covestro és a Holland Királyi Haditengerészet mérnökei szintén ezt a kérdést próbálták kideríteni.
De nem hagyományos módon...
Az anyagok szakítószilárdságát hagyományosan szakítóvizsgálattal mérik meg. Mint a fémeknél a 3D nyomtatás alapanyagainak vizsgálatakor kinyomtatnak egy kis mintát, és az erre célra kifejlesztett szakítógéppel egymásnak ellentétes irányban kifejtett húzó erő hatására elszakítják az anyagot. A töréskor a középponti metszéspont felületével felosztott részre vetített erő fogja kifejezni annak erejét.
Noha ezek a számok sokat jelentenek a mérnökök számára, de mint mondják, " a puding próbája, hogy megeszik".
A Covestro, a Holland Királyi Haditengerészet és az Ultimaker egyedülálló együttműködésbe kezdett, melynek célja, hogy felemeljenek valami komoly súlyt. Így valódi képet kaphatnak arról, hogy milyen erősek lehetnek a 3D nyomtatott alkatrészek.
De mi lehetne a legjobb szemléltető eszköz? Edzőtermi súlyok? Egy motorbicikli? Egy autó? Talán egy nagy dzsip? És akkor a holland királyi haditengerészet megkérdezte:
Miért nem egy páncélozott jármű?
A kezdeti terv elkészítése
Ahhoz, hogy egy nehéz járművet 3D nyomtatott alkatrész segítségével megemeljünk, először elemeznünk kellett a megemelendő tárgy paramétereit!
Miután az acélgyűrűk geometriáját importálta a CAD-szoftverbe, az Ultimaker alkalmazásmérnöke, Lars de Jongh elkészítette a kapcsolószem CAD modelljét. Lars először meghatározta a tervezési követelményeket:
- A stabil 3D-s nyomtatáshoz a kapcsolószem alkatrésznek lapos oldala kell legyen.
- A kapcsolószemet úgy kellett kinyomtatni, hogy a rétegvonalak ugyanabban az irányban lessenek, mint az összekapcsolt alkatrészekre vetített erők iránya.
- A nyomtatott alkatrész érintkező felületeinek és a fémgyűrűk kölcsönhatásban lévő felületének az erők egyenletes eloszlásához a lehető legnagyobbnak kell lennie.
A megfelelő anyag kiválasztása
Az Ultimaker Marketplace tele van több száz 3D nyomtatáshoz használható alapanyagokkal. Az alapanyag tulajdonságok szűrőinek beállítása alapján tulajdonságok egyedi kombinációjával nagy valószínűséggel megtalálja az Ön alkatrészének megfelelő anyagot.
A teszthez szükséges alapanyagnak rendkívül erősnek kellett lennie, de képesnek kell lennie arra is, hogy elnyelje a rövid ideig tartó maximális erőket, tehát némi rugalmassággal is rendelkeznie kell. A Covestro Addigy® F1030 CF10 megfelelt a beállított követelményeknek. Ez a nylon alapú polimer szénszállal van feltöltve, és az Ultimaker S5 és CC nyomtatómag segítségével nyomtatható.
A tervezés optimalizálása szimulációk segítségével
Egy tömör, 2 kilogrammos alkatrész 3D-s nyomtatása kevesebb időt vesz igénybe, mint a hagyományos módszerekkel történő gyártása. A helyes geometria érvényesítéséhez szükséges iterációk száma azonban azt jelentette, hogy az idő továbbra is tényező volt. Ezért a tervezést a nyomtatás előtt számítógépes szimulációkkal optimalizálták.
A Covestro digitálisan alkalmazta a tervezésre ható erőket olyan szoftver segítségével, amely ismeri a szénszálas nejlon anyagának pontos fizikai tulajdonságait. A szimulációk futtatásával azonosítani tudták, hogy hol kell módosítani a tervezést, és hol lehet eltávolítani az anyagot. Ezzel egy olyan optimalizált kialakítást hozott létre, amely nagyobb súlyt tudott emelni, miközben kevesebb anyagra volt szükség, ami gyorsabb gyártási időt eredményez, kevesebb költséggel.
A szimuláció ellenőrzése
Mielőtt felemelhettük volna nehéz járművünket, fizikailag ellenőriznünk kellett a nyomtatott alkatrész számított szilárdságát. Két mérethez két terv készült. Az első egy 1 kilogrammos láncszem volt, amely becsléseink szerint 12 tonnának tudott ellenállni. A második, nagyjából 2 kilogramm súlyú a becslések szerint 38 tonnának tudott ellenállni. A Holland Királyi Haditengerészetnek van egy helyszíni ipari szakítószilárdság-vizsgálója, amely akár 343 kilonewton erőt is képes kivetíteni egy tárgyra. Mind a kezdeti, mind az optimalizált verziót tesztelték a nagy és a kicsi verzióra.
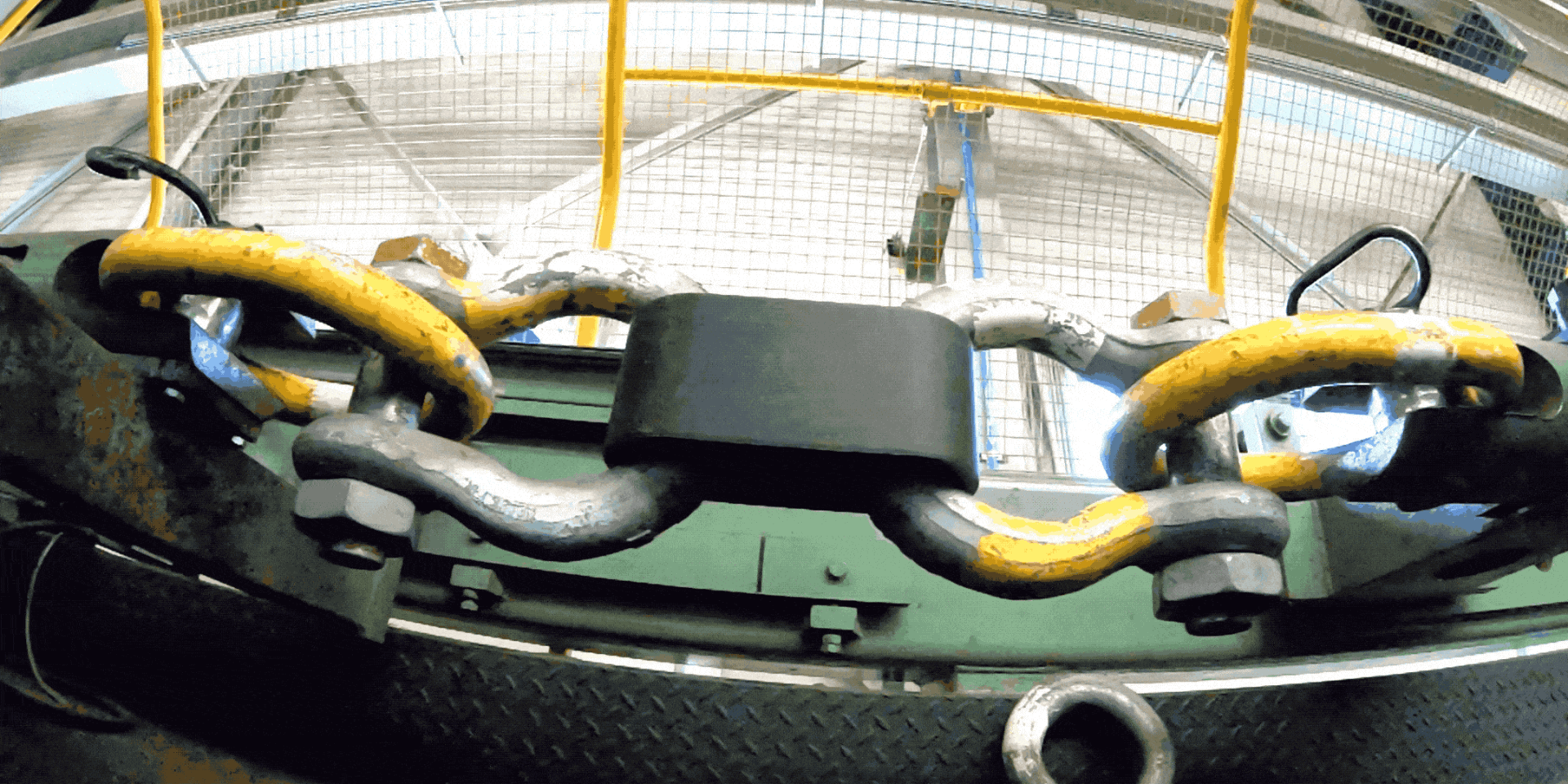
Az optimalizált kialakítás eredményeként a nyomtatott alkatrész nagyobb erőt tudott elviselni, miközben a súlya harmadával kisebb volt. A tesztek egyik eredménye, hogy a szimuláció által kalkulált paraméterek és a mért eredmények között a különbség átlagosan mindössze 1%-os volt. Ez a munkafolyamatot pontossá és nyereségessé tette, mivel a tervezéshez használt információk a méréseknek és a szimulációknak köszönhetőek pontosak voltak.
Két jármű felemelése
Több hónapos tervezés, nyomtatás, tesztelés és tervezés után eljött a cselekvés ideje! Két láncszem és a műanyag összekötőszem egy katonai nehéz járművet készült felemelni. A holland hadsereg dél-hollandiai bázisán a 13. könnyű Rhino-dandár segített nekünk páncélozott mentőjárművével. A Leopard 2 "Buffalo" elejére egy daru van felszerelve, mely nehéz járművek, például teherautók és harckocsik emelésére szolgál. Bemelegítésként az 1 kilós láncszemet egy 2 tonnát meghaladó tömegű Mercedes dzsip katonai változatának emelésére használták. Egyáltalán nem volt probléma: a jármű könnyen felemelhető volt.
Aztán eljött az ideje valami nagyobbnak...
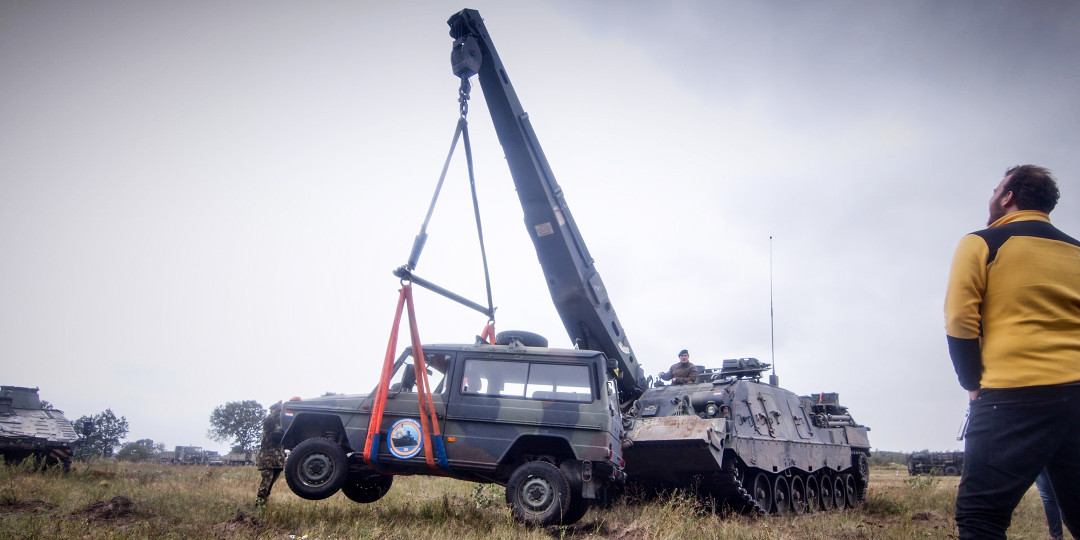
Az M113-as páncélozott jármű és a Buffalo daru közé helyezték a 2 kilós tömör szénszál erősítésű nejlon összekötő láncszemet. A fémgyűrűket a helyükre húzták, és négy kábelt erősítettek az alsó horogtól a járműhöz. A daru lassan elindult felfelé, megfeszítve a kábeleket és a 3D nyomtatott részt. Aztán a 12 tonnás jármű lassan felemelkedett, a föld felett lebegve, egy 3D-s nyomtatott alkatrészen lógva! A Buffalo daru körbehajtott, hátra, előre, megfordult, de a nyomtatott alkatrész tökéletesen kitartott.
Az együttműködés nagyon sikeres eredményt hozott.
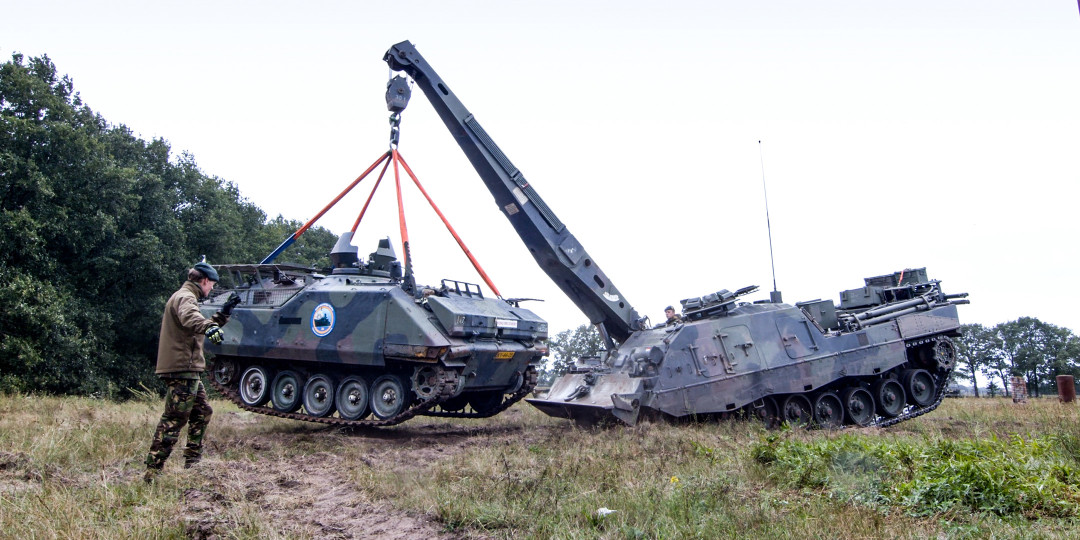
Tanulmányok és legfontosabb tudnivalók
Lenyűgöző volt látni, hogy a CAD-szimulációktól a megvalósításig eltel út során, a mérnökök nemcsak egy formát szimuláltak, hanem pontos előrejelzéseket is adtak, figyelembe véve az alapanyagot, sőt a szálirányt is. Az ilyen eszközökre való támaszkodás komoly előnyt jelent a mérnökök számára a hirtelen jött problémák megoldására.
Bár minden alkatrészt megfelelően karbantartott helyiségben nyomtattak, és az anyagok nem voltak kitéve nedvességnek, mégis észrevehető különbség volt a szárazraktárban nyomtatott változatok és a szándékosan szárított filamentorsóval, fűtött, száraz nyomtatószobában nyomtatott részek között. A nejlon felszívja a nedvességet, és ez gyengébb nyomatokat eredményezhet. Ezért nagyon fontos ismerni az anyagok tulajdonságait, és ennek megfelelően kezelni őket.
Hiszem ha látom
A műszaki adatlap absztrakt számokban mutatja meg az anyag szilárdságát. De ha látja, mit lehet elérni erős és optimalizált 3D nyomtatott alkatrészekkel, könnyebb megérteni az additív technológia lehetőségeit, és ihletet meríteni új és izgalmas alkalmazásokhoz. Ezért javasoljuk, nézze át a Miért 3D oldalunk tartalmát!
Célunk, hogy a technológia iránt érdeklődő szakemberek a külföldi példa által meg- és felismerhessék a lehetőségeket!
2022.11.01. Forrás: Ultimaker.com
Esetleges fordítási hibákért elnézést kérjük, azokért felelősséget nem tudunk vállalni.